Project Profile: Butler Farms

Photo Credit: Butler Bioenergy


Key Features



Highlights
- Covered lagoons help control rainwater run-off and significantly reduce odor.
- 180 kW genset produces electricity and heats the digester.
- On-site microgrid uses electricity generated from biogas along with recently installed solar array.
Butler Farms, located in Lillington, North Carolina, is a swine finishing facility that has been operating since 1995. In 2008, the farm covered two lagoons, primarily to address neighbor complaints about odor. Captured biogas from the lagoons was flared until a new anaerobic digestion (AD) system was installed in 2012, at which point the facility began generating electricity with the captured biogas.
Overview
“Renewable energy is not a tree-hugger thing. It’s just a sensible thing to do with your waste.”
– Tom Butler, Butler Farms
Butler Farms’ 10 barns house approximately 8,000 hogs that feed the covered lagoon digester. At capacity, the operation produces around 10,000 gallons of manure daily. The two covered lagoons from the original system, which collectively cover an area of about four acres, serve as overflow lagoons for the main digester’s effluent in the current system.
Currently, the AD system only digests manure, but the farm is working on a system to co-digest off-farm food waste to boost biogas production.
System Details
The digester is an 18-foot deep, covered earthen lagoon lined with a synthetic liner. At 190 feet long and 85 feet wide, it has a volume of approximately 1 million gallons. It receives manure from approximately 1.5 swine barn pits daily and has about a three-week retention time, after which the sludge is drained into the farm’s two larger overflow lagoons. Butler Farms is currently exploring solids separation options to address the overflow lagoons’ limited sludge capacity. To optimize the digestion process, the digester contents are mixed and kept in the mesophilic temperature range of 95°F to 105°F. As part of their plan to implement co-digestion of off-farm food wastes, the farm has equipped the digester with a 20,000-gallon mixing tank.
Butler Farms collects an estimated 12 million standard cubic feet per year of biogas from both the main digester and the overflow lagoons. If co-digestion is implemented, the farm expects the biogas yield to significantly increase (up to 3 to 10 times, depending on the waste used). A scrubber removes hydrogen sulfide from the biogas, which then goes to a 180 kW genset, generating approximately 545,000 kWh of electricity annually. The facility uses waste heat from the genset to heat the digester.
Biogas Use

Photo Credit: Butler Bioenergy
Biogas from the two original covered lagoons was originally flared. The farm was able to generate credits from their carbon offset, but the carbon credit market plummeted in 2009, significantly decreasing their expected revenue from carbon credit sales.
When they installed the new covered lagoon digester in 2012, Butler Farms entered into a power purchase agreement with their electrical utility, South River Electric Membership Corporation (EMC), to sell the renewable energy they were generating. They also installed a 20 kW solar array and began selling the solar power to South River EMC.
In 2017, the farm partnered with both South River EMC and North Carolina Electric Membership Corporation (NCEMC) to develop an on-site microgrid. The microgrid uses the farm’s biogas generator and solar array, and they also have a 100 kW standby diesel generator which can serve as a backup for the system. NCEMC provided a 250 kW/735 kWh battery storage system and a separate controller used to integrate and manage the project’s components, while South River EMC provided interconnection equipment. The controller allows NCEMC to isolate the farm from the larger electric grid in the case that islanding is needed, and they can selectively isolate the surrounding areas from the utility as well. The battery enclosure was designed to accommodate North Carolina’s hot summers and cold winters while ensuring that the system remains within the recommended operating temperatures to prolong battery life.
Under normal conditions, the microgrid connects to South River EMC’s distribution system to add renewable energy to the traditional energy sources supplied by the grid. In the case of an outage, the microgrid can also operate independently and provide power to the farm and surrounding homes, which helps avoid prolonged outages following severe weather events. This introduces increased stability to the local electricity supply and allows the farm to give back to the community.
Benefits
Butler Farms advances sustainability in the following ways:
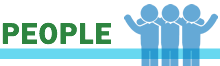
- Reduces odor from hog manure previously contained in open lagoons
- Protects human health by reducing pathogens in manure through the anaerobic digestion process
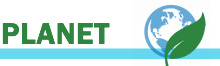
- Reduces methane emissions from manure management
- Offsets the use of fossil fuels
- Will divert food waste from landfills through planned co-digestion of food waste
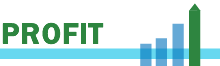
- Generates marketable carbon credits for greenhouse gas emission reductions
- Generates revenue from electricity sales
System Design Properties
Property | Value |
---|---|
Feedstock Processed | Swine waste |
Digester type | Covered lagoon |
Population Feeding Digester | 7,890 finishing hogs |
Baseline System | Storage Lagoon |
System Designer and Developer | 2012: Martin Construction Resource LLC (formerly RCM) 2008: Environmental Fabrics, Inc. |
Biogas Generation | 32,000 ft3/day |
Receiving Utility | South River EMC |
Biogas Uses | Electricity |
Genset Output | 180 kW |
System Financing
The total turnkey cost of the digester and its auxiliary equipment (e.g., mixing tank, lagoon cover, genset, hydrogen sulfide [H2S] scrubber) is estimated to be $550,000 to $650,000. Butler Farms relied on the following grants, cost-sharing, and cash reimbursement agreements to cover the up-front capital and operating and maintenance (O&M) cost of the digester:
- A combined $373,780 grant from the North Carolina State Energy Office and the North Carolina Green Business Fund (both grants were administered at the state level, but ultimately the funds were derived from the federal-level American Recovery and Reinvestment Act [ARRA]);
- A $116,480 cost-sharing agreement from the United States Department of Agriculture’s (USDA) Natural Resources Conservation Service’s (NRCS) Environmental Quality Incentives Program (EQIP), a $20,000 grant from the North Carolina Farm Bureau Federation’s Farm Energy Efficiency Program (FEEP); and
- A 30 percent cash grant of eligible cost spent on the project from the ARRA Section 1603 Program.
Butler Farms estimates the total out-of-pocket cost of the digester at approximately $50,000 over the first year of operation. This out-of-pocket expense includes the remaining capital cost not covered by grants, cost-sharing, or cash reimbursements and the cost of operating and maintaining the digester over the first year. Butler Farms estimates that the annual O&M cost at about $25,000.
Recognition
In 2012, the Butler Farms biogas project was featured in The Travel Channel’s “Off Limits” program. In 2019, Butler Farms was given the Distributed Energy Award from POWER Magazine.
Pursuant to 5 CFR § 2635.702(c)(2), names are displayed here as the result of recognition for achievement given under an agency program of recognition for accomplishment in support of the agency’s mission. Any reference to a specific company or commercial product or service by trade name, trademark, manufacturer, company, or otherwise does not constitute or imply the endorsement or recommendation of EPA.