Steps to Safe Renovation and Repair Activities
This information highlights precautionary measures and best work practices for conducting repairs or renovations in older buildings that have PCB-containing building materials, but do not have an abatement planned. A building owner or contractor may be required to use additional safety measures based on individual building conditions.
On this page:
- Are you working on a renovation or repair project of a school or other building?
- Safety Considerations: Employ Protective Measures (Interior and Exterior)
- Comply with Occupational Protective Regulations
- Communication with Building Occupants/Third Parties and Site Security
- Set up the Work Area to Prevent the Spread of Dust
- During the Renovation, Use Tools that Minimize the Generation of Dust and Heat
- Leave the Work Area Clean
Are you working on a renovation or repair project of a school or other building?
You need to know how to work safely with potentially contaminated building materials. This information will help contractors and building owners plan for renovation and repair projects that could disturb caulking and other building materials potentially contaminated with PCBs. Following the work practices discussed in this section will help reduce the exposure risk to workers and building occupants to PCBs. The following suggested work practices will assist:
- Employ protective measures during a renovation
- Leave the work area clean and safe for building occupants after completing the job
- Properly disposing of waste materials
Safety Considerations: Employ Protective Measures (Interior and Exterior)
Depending on the type of building, scope of the project, and the potential volume of dust generated by the corresponding work methods, you should consider employing various protective measures. Protective measures provide direct personal protection of workers, protection of building users, and third parties (e.g., students, teachers, and passers-by). They also safeguard against spreading PCB dust to other surrounding areas of the renovation project.
Comply with Occupational Protective Regulations
The Occupational Safety and Health Administration (OSHA) regulations at 29 CFR 1926.28(a) state that, "The employer is responsible for requiring the wearing of appropriate personal protective equipment in all operations where there is an exposure to hazardous conditions." This means you should use suitable personal protective equipment (PPE) for dust-generating work methods.
The following generally applicable PPE should be considered:
- chemical-resistant gloves
- Tyvec disposable coveralls and shoe covers
- safety glasses or protective goggles
- respiratory protection
These protective measures should be sufficient to prevent PCBs from entering your body through inhalation, oral ingestion and/or dermal contact (absorption through exposed skin).
In addition, worker hygiene is an important protective measure. Eating, drinking, and smoking should be prohibited in the work site. For work involving significant dust generation, showers and separate changing cabins for work clothing and everyday clothing should be provided.
Communication with Building Occupants/Third Parties and Site Security
Depending on the type of building, scope of the project, and the potential volume of dust generated by the corresponding work methods, you should consider employing various protective measures. Protective measures provide direct personal protection of workers, protection of building users, and third parties (e.g., students, teachers, and passers-by). They also safeguard against spreading PCB dust to other surrounding areas of the renovation project.
Notify Building Occupants of the Work to be Performed
Protective measures for building occupants and third parties are critical when your renovation and repair project may disturb materials that are potentially hazardous. Clear communication with all affected groups (e.g. building occupants, workers, building owners, and community members) is necessary to create a safe working environment. For example, you should continually inform the affected groups of the following:
- the goals, type, and length of the renovation activities
- health and safety aspects of the project
- site access requirements and limitations
Keep a Secure Work Area
You should also use site security measures to prevent unauthorized personnel form having access to the work areas until after the final cleanup. Examples of security measures include the following:
- Lock fence gates or doors to the work areas during off hours.
- Place signs, barrier tape and/or cones to keep all non-workers out of the work area. For apartment buildings or other dwellings, keep pets out of the work area to prevent them from tracking contaminated dust and debris outside the work area. Signs should be in the primary language of the occupants and should say "Do Not Enter - Authorized Personnel Only" and "No Eating, Drinking, or Smoking."
- Establish a system to identify authorized personnel and any limitations to their approved activities.
- Provide a means for approving all visitors to the work area, and ensure trained site personnel accompany visitors at all times with appropriate PPE.
Set up the Work Area to Prevent the Spread of Dust
When working on a renovation or repair job with the potential for PCB-containing caulk and other building materials, appropriate controls should be put in place to minimize spreading dust during the renovation and/or repair activity. At a minimum, consider separating work areas from non-work areas and select appropriate PPE and tools.
The work area should be protected by constructing a containment area whenever potentially hazardous material is disturbed and could generate dust. Plastic sheeting can be applied to the floor, ground or other applicable surfaces to prevent contaminating the building interior or exterior from dust generated by the work. Construct the containment area so that all dust or debris generated by the work remains within the area protected by the plastic. Placing the containment area under negative air pressure is also an effective tool. EPA recommends using high-efficiency particulate air (HEPA) tools to minimize dust release. The size of the containment area and dust controls may vary depending on the size of the renovation or repair, the methods used, and the amount of dust and debris that will be generated.
Inside the Building
The following techniques can be employed to prevent/minimize the spread of PCB-containing dust when working inside the building:
- Remove items such as furniture, books, wall hangings, etc.
- Use heavy plastic sheeting (e.g., 4- or 6- mil plastic) to cover floors in the work area and secure with tape.
- Close all doors in the work area, including closet and cabinet doors, and cover with plastic sheeting. When the work area boundary includes a door used to access the work area, cover the door with two layers of protective sheeting as described in the following:
- Cut and secure one layer of sheeting to the perimeter of the doorframe. Do not pull the sheeting taut. Create a few folds to leave slack at the top and bottom of the door before taping or stapling.
- To allow workers access, cut a vertical slit in the middle of the sheeting leaving 6" uncut at the top and bottom. Reinforce with tape.
- Cut and secure a second, overlapping layer of sheeting to the top of the door. To allow worker access, do not secure the sides or bottom of the door.
- Close and seal the ventilation system in the work area with tape and plastic sheeting. This will keep dust from getting into vents and moving through the building. If possible, you should turn off your heating, ventilation and air conditioning (HVAC) system to prevent contaminating the system.
- Put all necessary tools and supplies on the protective sheeting in the work area before you begin work to avoid stepping off the protective sheeting before the work is complete
Outside the Building
When working outside the building, the following techniques can be employed to prevent/minimize the spread of dust and debris:
- Use heavy plastic sheeting to build an enclosure around the work area.
- Mobile scaffolding is a convenient frame for constructing such an enclosure.
- Utilizing a few two-by-fours and the door covering method described above, an entrance/exit to the enclosure can be created.
- Use heavy plastic sheeting to cover the ground within the enclosure. Secure with tape.
- Construct a decontamination area just outside of the enclosure by placing heavy plastic sheeting on the ground. This area is used to remove personal protective equipment and to clean equipment used in the enclosure.
For locations where a containment area cannot be constructed, the following techniques should be used, as appropriate:
- Cover the ground and plants with heavy plastic sheeting to catch debris. The covering should extend at least 10 feet out from the building. Secure the covering to the exterior wall with a wood strip and staples, or tape.
- Close windows and doors within 20 feet of the work area to keep dust and debris from getting into the building.
- Seal off any vents or air exchange systems into the building which are located within the work area.
- Move or cover any play areas within 20 feet of the work area.
- To prevent debris from falling beyond the 10 foot covering when working on the second story or above, extend the sheeting farther out from the base of the building and to each side of the area where materials are being disturbed.
- To prevent the spread of debris when work is close to a sidewalk, street, or property boundary, or the building is more than three stories high, scaffolding sides should be covered in plastic.
- Avoid working in high winds if possible. Otherwise, take special precautions to keep the work area contained when the wind is strong enough to move dust and debris. For example, a wind screen can be constructed of plastic at the edge of the ground-cover plastic to keep dust and debris from migrating.
After you construct an effective containment area, make sure you control the spread of dust outside your work area:
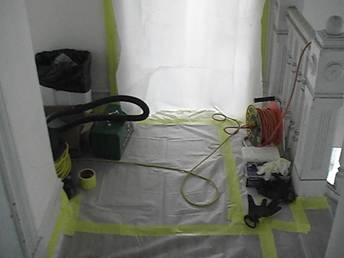
- Put all necessary tools and supplies on the protective sheeting in the work area before you begin work to avoid stepping off the protective sheeting before the work is complete.
- Remove or vacuum off Tyvec suits when exiting the work area so the dust stays inside the work area.
- Every time you leave the plastic sheeting, remove your disposable shoe covers, and wipe or vacuum your shoes, especially, the soles, before you step off the plastic sheeting. A large disposable tack pad on the floor can help to clean the soles of your shoes.
- Change out of your work clothing before going home, and launder non-disposable protective clothing separately from family laundry.
During the Renovation, Use Tools that Minimize the Generation of Dust and Heat
Select tools and work methods that generate the lowest possible dust volume.
Remember that you are creating dust as you scrape, drill, cut, grind, etc. You can breathe in this dust while you are working, or it can expose building occupants to contaminants as it settles.
PCB gases may be released into the air if your tools or work methods produce high heat (i.e., temperatures exceeding 212°F). This increases the risk for workers or building occupants to breathe in PCB gases. More comprehensive protective measures are necessary for methods that generate moderate to heavy amounts of dust or heat.
- Use tools that generate the least amount of dust and can still get the job done. Detailed information on tools can be found in Summary of Tools and Methods for Caulk Removal.
- Manual tools, such as utility knives, chisels, and scrapers, generate lower volumes of fine dust and less heat, but are primarily used for smaller joint lengths or when the joints are difficult to access for structural reasons.
- Electromechanical tools, such as oscillating knives, jigsaws, and rotary cutting tools, have ergonomic advantages over most manual methods, as they are better suited for projects with many joints and semi-soft to hard and brittle caulk; however, they generally generate higher volumes of dust and more heat, which requires more complex protective measures than manual methods.
- Grinding electromechanical tools generate large volumes of dust, and are therefore not recommended for the removal of potentially PCB-containing building materials, unless appropriate control measures are implemented (view the section on protective measures). Examples of such tools include angle grinders, masonry groove cutters, circular saws, and slot mills. Jigsaws and saber saws also lead to dust emissions, especially in the case of brittle caulk; furthermore, elastic compounds may gum up the saw blade.
- When using electromechanical tools tools, use HEPA vacuum attachments to contain the dust generated.
- For larger projects, use wet sanders and misters to keep down the dust created during sanding, drilling, and cutting.
Read additional information on tool selection and protective measures.
Leave the Work Area Clean
The work area should be left clean at the end of every day and especially at the end of the job. The area should be as free of dust and debris as possible. The following cleaning supplies, tools, and equipment you may need are available in hardware or garden supply stores:
- Heavy-duty plastic bags
- HEPA vacuum with attachments and a powered beater bar
- Masking tape, duct tape, or painters tape
- Misting bottle or pump sprayer
- Disposable wet-cleaning wipes or hand towels
- Detergent or general-purpose cleaner
- Mop and disposable mop heads
- Two buckets or one two-sided bucket with a wringer
- Shovel and rake
Daily Activities
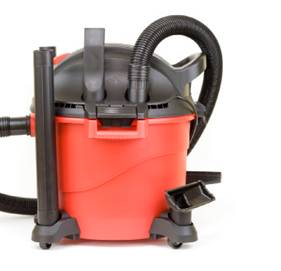
On a daily basis, renovators should:
- Pick up as you go. Put trash in heavy-duty plastic bags.
- Vacuum the work area with a HEPA vacuum cleaner frequently during the day and at the end of the day.
- Clean tools at the end of the day.
- Dispose of or clean off your personal protective equipment
- Note that waste water produced during the job from mopping, wet cleaning, cleaning of equipment, or misting may be regulated for disposal by State and/or Federal authorities.
- Continue to separate the work area from the rest of the building and remind occupants to stay out of the area.
End of the Project Activities
- When the job is complete, repair workers and/or renovators should:
- Vacuum any exposed surfaces, including walls and ceilings, with a HEPA vacuum cleaner.
- Consider misting dusty sections of the plastic sheeting with water before taking them down. This will keep dust from becoming airborne again.
- Remove plastic sheeting carefully, fold it with the dirty side in, tape it shut, and properly dispose of it.
- Vacuum all surfaces again with a HEPA vacuum cleaner.
- Scrub the work area with a general-purpose cleaner on a wet rag or mop until dust and debris are removed.
- Visually inspect your work to ensure that no dust or debris is present.
- Re-clean the area thoroughly if you find dust or debris.