Controlling Pollutants and Sources: Indoor Air Quality Design Tools for Schools
- Introduction
- Controlling Indoor Sources
Introduction
To protect indoor environmental quality the designer should understand indoor air quality problems and seek to eliminate potential sources of contamination that originate from outdoors as well as indoors by:
- Designing barriers to infiltration of outdoor pollutant sources into the school
- Selecting low-toxicity, low-emitting, moisture-resistant materials that can be safely installed and maintained
- Specifying the required sequence of work (for example, installing soft finishes after painting)
- Specifying the required duration of ventilation during and after installation
- Protecting ducts and the ventilation system during construction or renovations
- Ensuring that requirements are included in all pre-design, design, and construction documents
Typical Sources of Indoor Air Pollutants
Outdoor Sources | Building Equipment | Components/Furnishings | Other Potential Indoor Sources |
---|---|---|---|
Polluted
Nearby Sources
Underground Sources
|
HVAC Equipment
Non-HVAC Equipment
|
Components
Furnishings
|
|
Controlling Indoor Sources
Strategies for controlling indoor pollutant sources include:
- Materials Selection
- Installation Sequencing
- Material Encapsulation
- Materials Minimization
- Ventilation Techniques
- Air Cleaning
1. Materials Selection
- Strategies and Processes for Materials Selection
- Categories of Materials to Consider from an Indoor Air Quality Perspective
When selecting materials for interior surfaces and finishes for a high performance school, designers look for cost-effective, durable and materials-efficient products that provide the desired acoustical performance and aesthetic qualities, and protect indoor air quality and health.
Materials selection affects many other high performance goals in addition to indoor air quality. This site does not attempt to address these other factors and readers are encouraged to explore links to green sustainable products for buildings.
Potentially important sources of IAQ contaminants are interior building materials, office furniture, and equipment. Interior building materials — including carpets, carpet padding, paints, sealants and caulking, adhesives, floor and ceiling tiles, cabinets, molding, composite wood products, and other wood work — can contain contaminants that are gradually emitted (off-gassed) throughout the life of the material. The contaminants include volatile and semi-volatile organic compounds (VOCs and SVOCS, respectively), and small particulate substances that act as eye or throat irritants. Additional IAQ contaminants can originate with office furniture, room dividers, and photocopiers.
The selection process should consider installation and maintenance requirements as well as how the material or furnishing performs during its service life. Many benign finishes must be installed using adhesive, sealants or coatings that emit ("off-gas") VOCs during and after installation. Some VOCs are odorous, irritating, or toxic. It is important to select products whose emissions are low and the least hazardous or offensive.
From an indoor air quality perspective, the designer should generally seek to select materials that:
- require the use of the least toxic, low-VOC, water-based adhesives and coatings constituents;
- emit little or no odor;
- are easy to clean and maintain; and
- are not susceptible to moisture damage that can foster mold growth.
Strategies and Processes for Materials Selection
- Prioritize sensitive program areas. Identify and prioritize spaces where material selection issues are of particular concern based on intended occupancy, such as the nurses' office, and special education classrooms.
- Use product consensus standards when possible. Select products based on available consensus standards (developed by government agencies, environmental certification services, or trade organizations) that address health/toxicity issues relating to specific material types. NOTE: With the exception of a non-regulatory action level for radon in buildings (4 picocuries per liter (pCi/L) in air), EPA does not establish acceptable levels for pollutants in indoor air.
- Develop specification criteria. Facility planners should provide specification criteria for appropriate materials and installation methods. Incorporate specifications into design and construction documents.
- Obtain Material Safety Data Sheets (MSDS) and/or manufacturer certifications. For materials that are deemed critical to the project and for which standards or other references do not exist, obtain and review MSDS and/or manufacturers' certifications or test data. Contact manufacturers for clarification as needed. Review by experienced indoor air quality professionals may be justified for particularly critical materials or sensitive spaces.
- Require field approval for product substitutions. Review and approve contractor requests for product substitutions to ensure that the indoor air quality criteria defined in the specifications have not been compromised. Require MSDSs and other certifications for any product substitutions affecting critical items. Require justification from contractors for substitutions that do not meet environmental performance criteria. However, do not prohibit substitutions. Specialized subcontractors can be an excellent source of information about new and improved product alternatives. The approval process for substitutions should be clearly spelled out and should require specific product ingredient information, as well as information about any adhesives, solvents or other materials that might be used during installation or maintenance.
Categories of Materials to Consider from an Indoor Air Quality Perspective
- Flooring
- Wall and Ceiling Materials
- Paints and Coatings
- Adhesives and Sealants
- Engineered Wood Products
Flooring
The two most commonly used floor covering types for general use in schools are carpet and resilient floor covering products. Carpet offers acoustical and comfort benefits that are generally not available with other floor coverings. Many schools prefer to use carpet in classrooms and administrative areas. Resilient flooring is used for high traffic areas including classrooms, hallways, cafeterias, art rooms, restrooms and anywhere liquid spills are likely.
While there is currently considerable debate about the most appropriate flooring material for use in schools, EPA recognizes that there are advantages and disadvantages to any flooring system. Regardless of floor covering type specified, regular and effective cleaning and maintenance is essential to keep the floor covering dry and clean. Designers should explicitly consider cleaning and maintenance issues when specifying flooring finishes for various uses in schools. Designers should also specify the use of entry mat systems of adequate design and size to trap soil, pollutants, and moisture that otherwise would spread into and throughout the building.
Carpet
New carpet systems (including adhesives used to adhere face fibers to backing materials, carpet cushion, and the adhesives often used to install carpets), like most new interior finishing materials, will off-gas VOCs for a period of time after being installed. These emissions can be significantly reduced, although not completely eliminated, in the first 72 hours through the use of proper ventilation techniques. With any floor covering system, low VOC emission products should be selected and used in school applications.
The Carpet and Rug Institute (CRI) has developed a program known as the CRI Indoor Air Quality Green Label Program (CRI "Green Label") to determine the level of VOC emissions from carpet, floor adhesives, and cushion products. The CRI Green Label attached to a carpet, floor adhesive, or cushion signifies that a representative sample of the product type has been tested by an independent laboratory and meets the requirements for each program established by CRI. While the CRI program has contributed to significant reductions in the emissions of certain compounds from carpets, it does not necessarily assure that emissions from carpet, floor adhesives, or cushion will not pose problems for some people. More recently CRI has developed Green Label Plus, an enhancement to the CRI Green Label which incorporates additional requirements to meet California's Collaborative for High Performance Schools (CHPS) low-emitting materials criteria. Products listed as CHPS-compliant materials have been chamber tested to meet the indoor air quality guidelines outlined in California's specification section 01350. Green Label Plus, in addition, incorporates on-going product testing.
Carpet also acts as a reservoir for dust, dirt, pollen, mold spores, pesticides and other materials which may originate indoors or be brought into the indoor environment from outside. If kept very clean from the time it is installed, carpet can trap a significant amount of particles, which can be removed through regular and effective vacuuming. However, inadequate maintenance can allow large quantities of dust and debris to build up in carpet. Some studies indicate that poorly maintained carpet can release significant quantities of particles into the air during the course of daily activity. In addition, young children may play on carpet where they may be more likely to come into contact with contaminants that have not been properly removed through regular and effective vacuuming.
If covering a large surface area, carpet and other fabrics can act as "sinks" for the adsorption of VOCs from other sources (during application of paint and other finish coatings, for example) and re-emit them later. To minimize the potential for VOCs to be adsorbed from other sources and re-emitted over time, sequence installation of soft surfaces such as carpet as late as possible and/or remove or cover all soft surfaces and use direct ventilation until the coating dries.
It cannot be over-emphasized that proper cleaning and maintenance is a critical component of any flooring system. To help ensure longer life, maintain appearance, and help protect indoor air quality, carpet requires regular vacuuming with a well-functioning vacuum cleaner equipped with strong suction and a high-performance filtration bag and periodic wet extraction cleaning. CRI has established a Green Label Vacuum Cleaner Indoor Air Quality Testing Program to identify vacuum cleaners that effectively remove soil, contain dust within the filtration bag and the machine itself, keeping it out of the air, and which don't damage the carpet.
Moisture trapped below a carpet (or behind wall coverings or other building components) can result in mold growth and the release of mold spores and mold metabolic products (microbial VOCs or MVOCs) into indoor air. Effective moisture control is critical to protect all building systems from the potential for mold growth. It is essential that concrete be sufficiently cured and dry before carpet is installed over it.
- If carpet is specified, select a carpet that:
- has been tested for VOC emissions under the CRI IAQ Green Label Plus testing program
- can be easily cleaned and maintained
- is constructed to prevent liquids from penetrating the backing layer where moisture under the carpet can result in mold growth
- can be easily removed without the use of toxic chemicals
- Where new carpet odor is a concern, require suppliers to unroll and air out carpets in a clean, dry warehouse before bringing them into the building.
- Specify the least toxic carpet adhesive system compatible with selected carpet product. Require installer to use the smallest amount of adhesive necessary to fulfill the manufacturer's performance specifications for that product. Alternately, specify tack-down carpet to eliminate gluing. Carpet systems which utilize adhesives may off-gas adhesive constituents through the carpet for extended periods of time.
- Air out space(s) where carpet has been installed for a minimum of 72 hours.
- In renovations, carpet installation should occur only when the school building is not in use. An exception would be for small installations in which the space can be exhausted directly to the outdoors causing the room to be under negative pressure relative to adjacent spaces in the building. Extra exhaust ventilation should continue for a minimum of 72 hours after installation.
- Do not install carpet near water fountains, sinks, showers, pools, or other locations where it may get wet.
- Follow recommendations from the Carpet and Rug Institute for installation (CRI 104: Standard for Installation of Commercial Carpet).
- Follow the carpet manufacturer's maintenance recommendations.
- All spills must be cleaned up immediately and thoroughly. If carpet becomes saturated with a clean water spill, extract the moisture and be sure the carpet is dry within 24 hours. Spills of other liquids require immediate extraction and spot cleaning as well as drying within 24 hours.
Resilient Flooring
Flooring type selection affects thermal comfort (carpet retains heat longer than resilient flooring, for example) and lighting (resilient floors with high light reflectivity enhance daylighting). Resilient flooring does not generally provide the acoustical benefits of carpet.
Resilient flooring materials, like most new interior finishing materials, will off-gas VOC's for a period of time after being installed. Adhesives used to install and materials used to maintain (i.e., cleaners, finishes, etc.) resilient flooring can also be a source of VOC emissions, although low VOC adhesives and maintenance materials are available. The impact of resilient flooring on indoor air quality varies by flooring material, installation method and maintenance procedures. Final selection will depend upon the application and cost constraints.
The Resilient Floor Covering Institute (RFCI) , in collaboration with Scientific Certification Systems (SCS), has developed the FloorScore IAQ Certification program. FloorScore is a voluntary, independent certification program that tests and certifies hard surface flooring for compliance with the indoor air emissions of volatile organic compounds (VOCs) criteria developed by the California Department of Health Services and included in the California Section 01350 program. SCS acts as the third-party certifier ensuring program integrity and independence. The Collaborative for High Performance Schools (CHPS) recognizes products certified under FloorScore for low-emitting materials credit in the CHPS criteria.
If resilient flooring is specified, select a floor that:
- Has been tested for VOC emissions under the RFCI FloorScore program
- Can be easily cleaned and maintained with low-VOC cleaners and finishes
- Can be installed with low-VOC adhesives and coatings to minimize the indoor air pollution load and health risks to both installers and occupants.
- Require installer to use the smallest amount of adhesive necessary to fulfill the manufacturer’s performance specifications for that product. (Note: In some applications, interlocked rubber tiles and heavy linoleum can be laid without adhesive.)
- Air out space(s) where resilient flooring has been installed for a minimum of 72 hours.
Flooring with high performance coatings ("low maintenance") should be considered to reduce maintenance costs and the use of cleaners and floor finishes. Low VOC cleaners and floor finishes are available. Be sure to consult with the flooring manufacturer when specifying maintenance materials. Use of the wrong maintenance materials can damage resilient flooring. To help ensure longer life, maintain appearance, and protect indoor air quality, resilient flooring requires proper maintenance.
Walls and Ceiling Materials
Acoustical wall and ceiling systems are widely used in schools for sound dampening. A variety of products are available including modular wall panels (textile and metal-covered), suspended ceiling tiles (t-bar ceilings), and surface mounted ceiling and wall panels. Ceiling tile (usually in a T-bar ceiling) is the most common ceiling finish in schools. Because of the large ceiling surface area, the likelihood of its being disturbed during modifications/renovations, and its contact with HVAC systems, it is an important product to consider for air quality and materials efficiency.
![]() |
Select formaldehyde-free acoustical ceiling and wall systems with recycled-content. |
![]() |
Where feasible, sequence work to avoid applying VOC-containing materials in spaces with exposed acoustical surfaces. |
![]() |
Require adequate ventilation during installation of finish materials that emit indoor pollutants. |
![]() |
Consult with the manufacturer before painting/coating any acoustical material. With most ceiling tiles, for example, the material loses its acoustical properties once it has been painted. |
![]() |
Coordinate placement of lighting fixtures and other equipment in ceilings to provide clear access for inspection and servicing of HVAC system air filters and other components. |
![]() |
Remove any wetted ceiling tiles from the site immediately to avoid mold contamination. |
![]() |
Avoid using ceiling tile and sprayed-on ceiling finishes containing asbestos or formaldehyde. |
Paints and Coatings
Most conventional paint and coating products off-gas volatile organic compounds (VOCs). These VOCs may be either ingredients that are added to the paint to enhance product performance and shelf life or they can be byproducts of the paint drying process. High quality, "low-toxicity," and "no-VOC" or "low-VOC" paint and coating products are now available. However, such paints may still contain or emit odorous, toxic, or otherwise undesirable compounds, such as formaldehyde and pesticides (i.e., fungicides and bactericides).
While a variety of "low-VOC" and "zero-VOC" paints are now available to choose from, they vary in cost, toxicity, and performance. Therefore, paint selection should consider VOC content as well as overall composition and required performance characteristics, including hide ability and durability. "Zero-VOC" or "low-VOC" paints may minimize the indoor air pollution load and may reduce any health risks to both workers and occupants.
Water-based acrylic latex paints are generally lower in VOCs than solvent-based paints. Water-based paints are generally safer to handle and can be cleaned up with water, reducing health risks to workers and minimizing/avoiding hazardous waste. Leftover latex paint may be recyclable, thus reducing waste.
![]() |
Specify least toxic, formaldehyde-free, zero-VOC or low-VOC paint that meets durability and other performance requirements. |
![]() |
Specify products containing no lead, mercury, hexavalent chromium or cadmium. Though regulations have nearly eliminated many toxic components from consumer paint lines, industrial and commercial paints may still contain them. Check the MSDS. |
![]() |
Specify isolation requirements (isolation of construction zones from completed zones to prevent cross-contamination; removal, coverage, or isolation of porous materials to avoid adsorption and subsequent re-emission of solvents, maintaining negative ventilation in construction areas). When sanding dried paint, a dust mask should be worn. |
![]() |
Review recommended duration between paint application and occupancy and review for compatibility with maintenance schedules/requirements. |
![]() |
When possible, schedule work during unoccupied periods or periods of least occupancy. Large projects should be scheduled during the summer vacation months or other breaks. The maintenance schedule should also factor in manufacturer recommended air temperatures for application. |
![]() |
Where possible, perform painting and stripping off-site or select materials with factory-applied finishes. |
![]() |
For on-site interior painting, cover surfaces (e.g., with plastic sheeting), such as fabric-covered furnishings, that may adsorb VOCs. Specify sequence of installation so that painting and other "wet" applications occur before installation of "fleecy" materials. |
![]() |
Consider constructing barriers (for example, walls or curtains of plastic sheeting) to help isolate portions of larger areas and minimize the distribution of dust and other pollutants. |
![]() |
Wipe down all surfaces with a damp cloth as soon as possible after completing all dust-generating work typically associated with surface preparation. |
![]() |
Carefully observe manufacturers' recommendation for cleanup, storage, and disposal, for paints, primers, and thinners. (Note: Some products are classified as "flammable liquids" under federal regulations and must be stored in a specifically constructed safety cabinet.) |
![]() |
Keep paint containers covered as much as possible during and following use to protect against VOC release. |
Adhesives and Sealants
Many conventional construction adhesives, sealants, "acoustic" caulking, grouts, and mortars used to bond structural components are solvent based and may off-gas large amounts of volatile organic compounds (VOCs) (including solvents and aromatic hydrocarbons).
![]() |
Use low VOC, low-toxic water-based, formulations which are now available for many applications. |
![]() |
Specify the least toxic/lowest VOC product suitable for the application and require the installer to use the smallest amount of adhesive necessary to fulfill the manufacturer's performance specifications for that product. |
Engineered Wood Products
School construction frequently uses pressed wood products in a variety of applications. These pressed wood products sometimes contain urea-formaldehyde, which may off-gas formaldehyde over a substantial period of time.
Engineered wood products include plywood, particleboard, and medium-density fiberboard (MDF). The principle uses of plywood include decorative wall paneling, doors, cabinets, and furniture. Particleboard is used for subflooring, wall paneling, cabinetry (core materials and shelving), cabinet tops, closet shelving, doors, and furniture. MDF is used in cabinet, furniture, and trim manufacture. Substitutes for these products include composite materials with no urea-formaldehyde; gypsum board for walls; solid wood or metal cabinets; solid wood, metal or plastic furniture; solid wood or metal doors; waferboard, oriented-strand board, iso-board, and phenol-formaldehyde bonded particleboard or plywood.
Materials can be obtained with lower potential formaldehyde off-gasing. Material formulation and pre-treatment can be effective in controlling formaldehyde emissions.
Barrier coatings and sealants (i.e., encapsulation) might be used to reduce formaldehyde emissions. It is important to recognize, however, that barrier coatings and sealants may pose their own indoor air quality problems. Adequate ventilation should be maintained during application and until the odor fades completely. Water-based coatings can help reduce VOC emissions.
Hardwood plywood or products containing hardwood plywood, should be certified to be in compliance with the Hardwood Plywood Manufacturers’ Association Voluntary Standard for Low Emissions (HPMA FE-86) and the U.S. Department of Housing and Urban Development (HUD) Standard 24 Part 3280 (related to the use of pressed wood products in manufactured homes). Specify only particleboard and medium density fiberboard (MDF), or products containing these substrates, that are third party certified to comply with the formaldehyde emissions requirements in ANSIproduct standards A208.1 and A208.2, respectively.
![]() |
Specify that all engineered wood products containing urea-formaldehyde bonding systems must be third party certified as meeting the particular ANSI standard for formaldehyde emissions. |
2. Installation Sequencing
Indoor air quality (IAQ) is affected not only by the materials that are used but also by the order in which they are installed. Certain materials and finishes (Type One materials) off-gas potential indoor contaminants for a short duration after they are manufactured or installed. The contaminants off-gassed by Type One materials can be adsorbed by "fuzzy" or "fleecy" materials as well as finishes (Type Two) that are woven, fibrous, or porous in nature. Type Two materials can become repositories (often referred to as "sinks") for substances that can be released much later or that promote subsequent mold growth. When possible, Type One materials should be allowed to dry before Type Two materials are installed.
![]() |
Specify air exchange rates and proper air filtration procedures for the ventilation system in construction documents to ensure that whenever possible, any necessary off-gasing from Type One materials has dissipated before Type Two materials are installed. |
![]() |
Require the contractor to properly clean all duct work and replace all air filters before building occupancy. |
Type One Materials:
- Composite wood products, specifically including particle board from which wood paneling, doors, or furniture may be fabricated.
- Adhesives, sealants, and glazing compounds.
- Wood preservatives, finishes, and paint.
- Control and/or expansion joint fillers.
- All hard finishes requiring adhesive installation.
- Gypsum board and associated finish processes.
Type Two "Fuzzy" Materials:*
- Carpet and padding.
- Fabric wall covering.
- Exposed insulation.
- Acoustic ceiling materials.
- Fabric covered acoustic wall panels.
- Upholstered furnishings.
*Materials that may be categorized as both Type One and Type Two are considered Type One materials.
3. Materials Encapsulation
Material encapsulation is the process of placing a barrier between the material of concern and the indoor air, thus reducing the amount of gases or particles that can be emitted into the indoor air from the product. Some encapsulation occurs automatically as a result of the building design, such as the wallboard and vapor barrier separating the insulation in the wall from the indoor air, and therefore would not require any further action.
If pressed wood products such as cabinets, shelves, and work surfaces contain any formaldehyde, all surfaces and edges (including door and drawer surfaces, and any drilled holes) should be thoroughly encapsulated to reduce the amount of pollutants emitted into the air. For durability, work surfaces can be covered with high-pressure plastic laminates. Factory applied coatings or films are generally good encapsulants. In the field, two or three coats of nitrocellulose or water-based polyurethane lacquer will greatly reduce emissions from smooth surfaces and edges. The websites of manufacturers of pressed wood sheet stock often contain detailed technical guidance on how to encapsulate their materials. Please note that it is usually less expensive to specify only pressed wood products that do not contain urea formaldehyde instead of attempting to encapsulate all surfaces.
4. Materials Minimization
For materials of concern that cannot be eliminated or encapsulated, try to use as little of the material as possible, within manufacturer's recommendations. For example, a smaller v-notch trowel would result in less adhesive being used, yet may still ensure enough adhesive for proper holding.
5. Ventilation Techniques
One of the major indoor air quality complaints in a new school is the odor from recently installed building materials and finishes such as flooring and flooring adhesives, paints and finishes, caulks and sealants, and cabinets and work surfaces made from composite lumber products. The most common cause of these is the release of gases, such as formaldehyde and a wide range of other volatile organic compounds (VOC's), from the products into the air. Through careful materials selection and material minimization, the designer can greatly reduce or even eliminate the need for air out and flush out.
Air out is when completed products that produce objectionable emissions are removed from packaging and unrolled or spaced apart in a well-ventilated warehouse so that fresh air can easily flow in and around the products, thereby quickly removing any pollutants emitted from the products. Drawers and doors of cabinetry should also be open, and electrical products such as computers and printers should be turned on. Because the products are being aired out in a well-ventilated warehouse, the pollutants are not emitted within the school building, thus reducing the chances that the pollutants will be adsorbed onto other building materials or finishes, or that occupants will be affected. The types of products most applicable for air out include rolls or tiles of synthetic flooring products, and products such as cabinets, shelving, desks, and work surfaces made from particle board, plywood, or medium density fiberboard (MDF).
Flush out is when large amounts of outdoor air are forced through a recently completed building for a period of 3 to 90 days so that the majority of pollutant emissions from building materials, finishes, and furnishings can be removed from the building before occupancy. The recommended minimum volume of outdoor air needed for flush out is the amount needed to ventilate the full school at least once each hour (1 ACH, or air change per hour), 24 hours a day, 7 days a week. At a minimum, all mechanical ventilation systems should be set to provide the largest amount of outdoor air as practical from the final construction stages when floor products and paints are applied through the first few days of occupancy. Based on a 90-day flush out of two different office buildings, the State of Washington now requires a minimum 30-day flush out period for all its new public buildings. California's building standards also require a 1 hour daily flush out prior to normal building occupancy to reduce contaminants that may build up when the ventilation is off overnight.
Exhaust or Spot Ventilation During Construction Activities
The size of exhaust fan needed will increase as the size of the room increases, and as the amount of gases being released into the air increases. The fan should provide about 5 air changes per hour (5 ACH). Divide the volume of the room in cubic feet by 12 to get the minimum amount of cubic feet per minute (CFM) that the fan must be able to exhaust. For example, a classroom with a volume of 9000 cubic feet (1000 square feet of floor area with 9 foot ceilings) divided by 12 results in a fan of 750 CFM. A 21 inch box fan may be sufficient for a single classroom if the materials are not too strong a source of gases, but would certainly not be sufficient for a wing or a whole school. As a rule of thumb, there may be enough airflow if odors do not spread out of the immediate area where the work is being performed, of if dust or smoke released into the air can be seen to be drawn towards the exhaust fan. As long as the odors or air pollutants are present, the temporary exhaust ventilation must continue to be operated, even during nights and weekends if necessary. Ventilation should continue for a minimum of 24 hours after completion, or until there are no longer any noticeable odors.
Exhaust or spot ventilation uses fans to mechanically pull polluted air from the building and exhaust it to the outside during construction or renovation activities. It is important that a fan be used to pull the polluted air out of the building, not to push outdoor air into the building. Simply opening windows or doors is not enough to effectively exhaust contaminants in most cases.
The fan should be placed in a window or exterior door as close to the work area as possible, and any openings in the window or door around the fan should be temporarily sealed with plastic or cardboard. Then open a window or exterior door at the opposite end of the room or building, so that fresher outdoor air will flow across the work area and sweep polluted air out through the exhaust fan.
For additional information on areas in schools where special exhaust ventilation is desirable on an on-going basis such as janitor closets, copy/work rooms and arts/crafts preparation areas where off-gasing from significant quantities of material may occur.
6. Air Cleaning
The use of air cleaning devices, other than particle filtration employed in the HVAC system, is generally not required if appropriate attention to controlling and managing sources of pollution and providing adequate ventilation are addressed in the design process. For additional information on air cleaning devices see Residential Air Cleaners (Second Edition): A Summary of Available Information.
- Gaseous Contaminant Removal
- Ozone Generators that Are Sold as Air Cleaners: An Assessment of Effectiveness and Health Consequences
Preventing the Entry of Pollutants from Outside the Building
Simple yet effective barriers can be designed and installed to significantly reduce several air pollutants from entering the building. These pollutants include radon and other soil gases from beneath the building, sewer gases from malfunctioning plumbing traps and vents, as well as allergens, pesticides and other contaminants brought into the building on shoes, and through openings to utility tunnels and crawlspaces.
- Radon Barriers
- Sewer Gas Barriers
- Entry Mat Barriers
- Shell Penetration Barriers
- Location of Air Intakes and Exhaust
- Integrated Pest Management
Radon Barriers
If the school is being constructed in a county with a high potential for radon (Zone 1 and other radon-prone areas that have been identified in Zones 2 and 3), preventive design and construction measures should be taken so that an inexpensive remediation system can be installed if radon levels are too high after the school is completed. EPA also recommends that this map be supplemented with any available local data in order to further understand and predict the radon potential of a specific area.
- Read more about radon.
- Check the EPA Map of Radon Zones to get specific information about your county and state.
- Contact your state radon coordinator to see if your state has more detailed information available, see Find Regional and State Indoor Air Quality Contact Information.
Generally, the source of radon gas is from the ground beneath the school. It flows into the school through cracks and openings when the air pressure inside the school is lower than the air pressure outdoors. Typical cracks and openings include the joint where the floor meets the wall, expansion joints in the floor, openings in the floor for the passage of pipes and wires, and hollow masonry walls that penetrate the floor. Since it cannot be determined before construction whether radon will be a problem, it is cost-advantageous in high radon potential counties to take the following precautions:
![]() |
Install 4 inches of 1/2 to 1 inch clean aggregate and a vapor barrier under all slab areas. |
![]() |
Install one centrally located sump pit per 100,000 square feet of earth-contact floor area. |
![]() |
Install a 6 inch PVC vent pipe from the sump pit to the roof. |
![]() |
Install a 120 VAC, 15A weatherproof junction box on the roof next to the 6 inch vent pipe, to permit installation of a fan to vent soil gas if post-construction testing finds elevated radon levels. |
![]() |
Seal all major slab openings, cracks, or penetrations with polyurethane sealant. |
![]() |
Make post-construction radon measurements using EPA's radon measurement in schools protocol. See radon publications for schools. |
These measures may cost between $0.10 and $0.75 per square foot of floor area that is in contact with the earth. If the gravel and vapor barrier are already being installed due to code requirements, the cost will be at the low end of this range. For important details on the design and installation of radon prevention or remediation systems, and radon health effects, see Radon Prevention in the Design and Construction of Schools and Other Large Buildings [EPA 625-R-92-016, June 1994]. See also Reducing Radon in Schools: A Team Approach [EPA 402-R-94-008, April 1994] at Publications about Radon.
Sewer Gas Barriers
Buildings have been evacuated due to a range of sudden and widespread health complications, only to find that the water in a simple drain trap has evaporated, or that a sewer vent is too close to an outdoor air intake, allowing sewer gases to enter the building. Sewer gases are more than just an odor problem; components such as hydrogen sulfide gas can, in sufficient concentrations, also cause health effects such as irritation of the eyes, nose and throat and difficulty breathing.
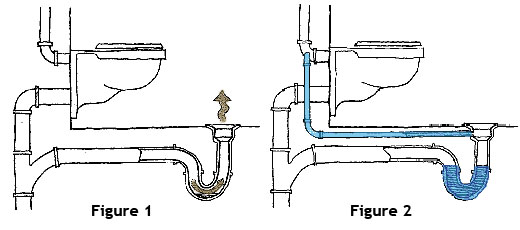
Figure 1: Standard traps can dry out, allowing sewer gases to enter the building.
Figure 2: Traps should be designed with automatic primers to prevent entry of gases.
Drain Traps
- Install automatic drain trap primers, available from several major manufacturers, in all floor drains to ensure that a small amount of water is periodically delivered to the trap, preventing the trap from drying out. Because of their continuous usage, drain traps in sinks, toilets, or drinking fountains are seldom a problem. Usually it is a floor drain in an obscure location, such as the mechanical room, shop area, or janitor's closet. Dry drain traps in mechanical rooms are especially problematic because the mechanical rooms often contain heating, cooling, and ventilation systems that can quickly spread the gases and odors to other parts of the building. This problem occurs not only in the drier western U.S., but also in the eastern U.S., so automatic drain trap primers are recommended for all areas of the country.
Sewer Vents
- Make sure sewer vents are not located where gases can be pulled back into the building or install an air admittance valve. Sewer vents, usually located on the roof, are sometimes located too close to an outdoor air intake for a ventilation system, or some other opening, which allows sewer gases to enter the building. The vent can be extended or moved so it is no longer a problem, or an air-admittance valve can be easily attached to the vent. Air-admittance valves are inexpensive for both materials and labor, and prevent sewer gases from exiting the vent. NSF International (www.nsf.org, formerly the National Sanitation Foundation) has conducted tests on these devices and all of the major building codes have approved their use.
Entry Mat Barriers
Entry mat systems are critical in trapping soil, pollutants, and moisture that otherwise would spread into and throughout the building, as well as in reducing the cost to properly maintain the building. Entry mat systems should be addressed during the design-phase of the building rather than as a maintenance issue after the fact. The International Sanitary Supply Association reports that most of the dirt within a building is tracked in on people's shoes, and that 85% of this can be removed if entry mats are properly designed and maintained. Without an entry mat system:
- entrances and lobbies can quickly become unsightly, providing a poor first-impression about the maintenance and condition of the building.
- dirt and pollutants can spread to larger areas, thereby requiring higher maintenance costs than otherwise would have been necessary.
- moisture tracked onto hard-surface floors can increase the chance of injuries and can reduce the life of carpet.
- increased grit tracked onto smooth-surface flooring can grind away the protective finish and carpets can quickly become loaded with pollutants.
Designing an Entry Mat System
To effectively remove most pollutants from shoes requires a combination of mat materials, textures, and lengths. The combination may vary depending on your climate and location. For example, a snowy climate may require a greater amount of scraper mat; a rainy location more adsorption mat; and a muddy location more of each of the mats.
![]() |
||
Scraper Mat | Absorption Mat | Finishing Mat |
Minimum of 6 feet long, and located outside the entry doors. Removes the bulk of dirt and snow with some form of knobby or squeegee-like projections. Generally the higher the projection, the better the cleaning and holding capacity. Surface mats are typically made of nitrile rubber. Recessed grating systems contain a deep well that will hold more dirt and moisture between cleanings, but will have a higher first cost. | Minimum of 6 feet long, and located just inside the entry doors. Generally made from nylon or combinations of nylon and heavily textured piles of polypropylene that can perform both a scraping action and a moisture wicking action. | Minimum of 8 feet long, and follows immediately after the absorption mat. Generally made from polypropylene with a course fiber surface that will both capture and hold any remaining particles or moisture. |
- The entry mat system should be at least 20 feet long, as wide as the entry doors, and employ three different types of matting.
- All mats should have anti-slip backings or other locking mechanisms to reduce sliding and tripping hazards.
- Since daily cleaning will be required, the ease of cleaning should be considered during selection.
Shell Penetration Barriers
- Seal all openings in walls, floors, and ceilings that separate conditioned space (heated or cooled) from unconditioned space. For example, it is common to punch large holes in the floor to allow pipes and wires to run between the rooms above and the crawlspaces or tunnels below. These oversized openings can cause two significant indoor air quality problems. Air that is contaminated with mold, radon, moisture, and pesticides can easily enter the rooms, and pests such as roaches or rodents can enter the rooms, leaving behind odors, allergens, and potentially, disease-causing pathogens.
References and Resources
- IAQ Tools for Schools Action Kit
- Building Air Quality: A Guide for Building Owners and Facility Managers
- National Clearinghouse for Educational Facilities (NCEF)
- Reducing Occupant Exposure to Volatile Organic Compounds from Office Building Construction Materials: Non Binding Guidelines. CA Department of Health Services.
- American Society of Heating, Refrigerating and Air-conditioning Engineers (ASHRAE). ASHRAE Standard 62, Indoor Air Quality.
- American Society for Testing and Materials (ASTM) Standard D5116-90, Small Scale Environmental Determination of Organic Emissions from Indoor Materials/Products
- The BEES (Building for Environmental and Economic Sustainability) software brings to your fingertips a powerful technique for selecting cost-effective, environmentally-preferable building products. Developed by the NIST (National Institute of Standards and Technology) Building and Fire Research Laboratory the tool is based on consensus standards and designed to be practical, flexible, and transparent. Version 4.0 of the Windows-based decision support software, aimed at designers, builders, and product manufacturers, includes actual environmental and economic performance data for 230 building products.
- American National Standards Institute
- Standards: ANSI A208.1-1993 (particleboard)
- ANSI "PBU,""D2"or"D3" (particleboard flooring);
- ANSI A208.2-1994 (medium density fiberboard);
- ANSI/HPVA HP-1-1994 (hardwood plywood)
- Carpet and Rug Institute Carpet In Schools
- Collaborative for High Performance Schools (CHPS): CHPS has developed a best practices manual to help schools, districts and practitioners to achieve high performance design, construction and operation.
- High Performance Building Guidelines, April, 1997, city of New York, Department of Design and Construction(PDF, 146 pp, 2.21 M)